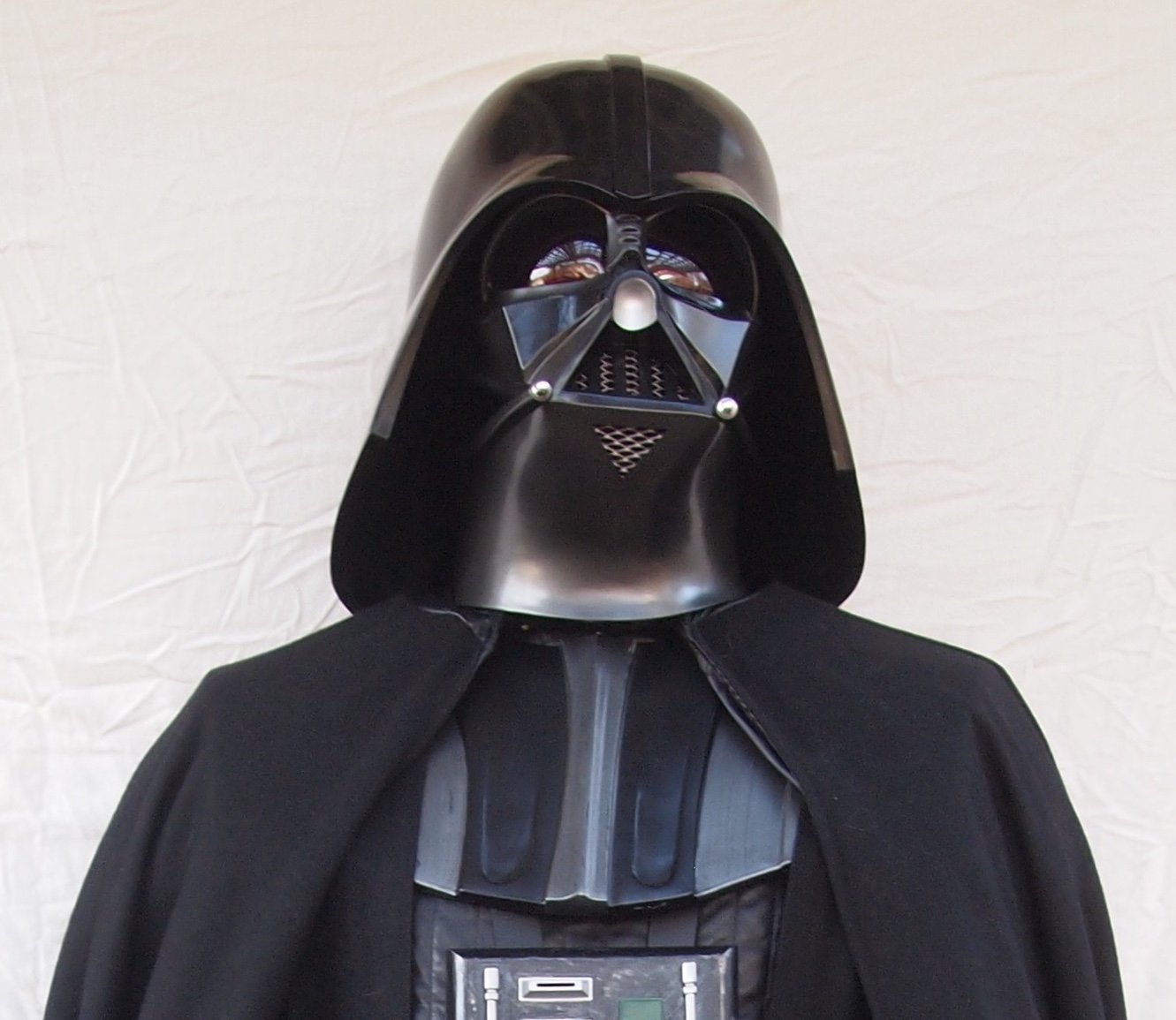
87ninefiveone
501st Reserve[501st]-
Posts
52 -
Joined
-
Last visited
About 87ninefiveone

501st Info
-
Name
Kal
-
501st ID
87951
-
501st Garrison
Carolina Garrison
Recent Profile Visitors
The recent visitors block is disabled and is not being shown to other users.
87ninefiveone's Achievements
-
That case is exceptional! Really nice work. Your thread needs to be bookmarked for others looking to 3D print this costume as well, lots of good info in here.
-
Looks great! Are you working on the inside of the case too?
-
That’s an interesting thought. Print it in TPU with high infill to allow some flex. Flex PLA might do it too. I wonder how well a painted finish would hold up to the flex though?
-
I had the same issue with the collar and I ended up cutting it in half about mid neck and attaching the front and rear portions to the armor separately. It’s not screen accurate, but it solves the issue and you can’t tell once your in costume with all the other stuff covering the neck area. Even printing in nylon that collar pierce is just too fragile to work as designed.
-
Looking good! You're weathering is outstanding, you should print and paint an extra bicep and submit photos for the medic CRL. In regards to the helmet buckle, I'm not sure if we have a really definitive reference shot of the actual prop or not. The only shots I've seen are dark and blurry screen grabs so I think the exact design is open to interpretation and the CRL isn't very descriptive other than that the buckle includes a tan colored square. I remixed Valok's buckle from Thingiverse for my build so it's similar in design to what the CRL shows, but I think the Facebook group buckle looks good and adds an extra bit of realism since it looks functional. If you're worried about approval, contact your GML to get their opinion before wasting time on finishing/painting.
-
I didn’t scale them at all them on my build as I thought they seemed in good proportion to the helmet and mask as is, but I didn’t scale the helmet or mask either. Yours looks fine from the shot you’ve posted. Any luck on dying the plasch?
-
Awesome build Ensi, impressive attention to detail! Congratulations on your approval!!! How did you find out that you’re number 26? I was kind of curious if I had the only mudtrooper in my area but couldn’t find a way to tell on databank.
-
Those goggles are too cool to scavenge from. The Sean Fields part isn’t totally accurate but that part would be super easy to model up. If you can get a nice clear top down and side shot next to ruler I’d be more than happy to model it for you. For printing the chest in PETG, make sure your bed is 70-80C and use a liberal coat of hairspray on glass (looks like a glass bed there?). I’d also go with about a 20mm brim to prevent lifting and make sure your printer isn’t near an A/C vent. PETG has a really tendency to lift on sharp corners. That and stringing are the major downsides to printing with it.
-
Thanks for the link to the hose! 6’ will be plenty, you'll probably end up at about 25-30” for each hose. Oh, and you’ve got a Carbon machine at work!!! Those things are crazy $$$. So many questions for you....super jealous of you’re bleeding edge equipment! I’ve got four machines to play with at work but they’re all FDM.
-
Great update! Either your printer is better or you’ve got way more patience than I do for sanding because you’re finishing work is spot on. Looking good. The chest plate fit looks about right, but what got me was the front to back distance which left a gap on top of the shoulders and at the sides (I printed with no scale adjustment and my chest circumference is 44 in). The shoulders gap is no big deal because it’s covered by the straps, but the side gap is a bummer. I would strongly suggest going slightly larger on the chest and back than you think you need to (maybe 3-5%). If you have measurements of yourself load up the STL files for the chest and back into meshmixer, fusion, or whatever. The way the files were sliced up by body the relative position of all the parts is preserved so you can scale them and check distances take sure everything will fit right (I didn’t realize this until after I printed them). Can I ask what hoses you ended up going with? My Russian gas mask hoses are a bit shorter than I’d like and I haven’t found a another source that looks right. Yours look pretty good.
-
Welcome aboard! I just finished a Sean Fields based build myself, let me know if you have any questions along the way.
-
Bummer on the shins. I can't believe they cracked from heat! Did that occur along a layer line or a glued part joint? If you reprint them find someone with a large bed so that they can be printed laying down and use PETG to get a bit more heat resistance and flexibility. The shins are going to get a lot of stress being strapped to the boot and will always be prone to cracking along part or layer lines if they're printed standing up. If printing them laying down isn't an option you might consider getting a sheet of 2mm ABS or styrene, cutting it to shape, and gluing it to the back of the shins as extra reinforcement. I did this on my printed chest and back armor and it stiffens things up considerably.
-
87ninefiveone’s Mudtrooper Build (Sean Fields - 3D Printed)
87ninefiveone replied to 87ninefiveone's topic in Mudtroopers
Thanks guys. I still have a lot of work to do to make the gear a bit more functional, but I’m pretty pumped to troop in it tomorrow! -
87ninefiveone’s Mudtrooper Build (Sean Fields - 3D Printed)
87ninefiveone replied to 87ninefiveone's topic in Mudtroopers
TX-87951 approved! https://imgur.com/gallery/55Vb6ab -
87ninefiveone’s Mudtrooper Build (Sean Fields - 3D Printed)
87ninefiveone replied to 87ninefiveone's topic in Mudtroopers
Thanks for the feedback guys. I went after the weathering last with a wet paper towel, magic eraser and a bit of sanding, but I'm not sure it improved things much. I'm still going to go ahead with submission after I get some suited up pics tonight, but I might be in for a repaint to get the effect right for approval. On the plus side I completed weathering of the soft goods which came out much better. I still went with some sponge dabbing, but I mainly used acrylic paint diluted down to 3-4 parts water to one part paint and did the application with a spray bottle that had an adjustable nozzle set for a coarse spray. I like the overall effect much better. If anyone is interested, I've 3D modeled quite a few small parts over the course of my build to save a few bucks and I've posted all of the parts to Thingiverse, you should be able to find them by searching my screen name or "mudtrooper". Here's a list of items I've made: 24mm hose connector for Sean Fields respirator Surefire M300 scope Large helmet buckle/greeble (design by Vahlok, but with curvature added). Large 40mm tri-glides for goggle strap Lower belt box set Imperial Officer belt boxes Respirator tri-glides and small Yugoslavian backpack buckle (modeled off the real part since I had them already) Shoretroooper/tanktrooper/mudtrooper 3" belt buckle A few final thoughts on 3D printing your kit. Total filament used was about 5.5kg of PETG/PLA. Around 230 hours of printing in total. The large armor parts can be printed at 0.2mm resolution using 25% infill and 4 perimeters (0.5mm line width). The goggles and respirator should be done with finer resolution, 0.1mm preferred to improve fidelity and reduce the amount of finishing needed. Be prepared to do a lot of reinforcing on the back side of the armor parts. I added ABS strips to the inside joints of the chest and back to prevent them from flexing/breaking and further reinforced a lot of seams with E6000. I still think going with a vac formed or fiberglass part is the way to go for the chest/back armor and will probably end up purchasing these in the future, but I ran out of time/money so the 3D printed parts will do for now. Build Cost Breakdown Pants/Coat (Jimiriquai), $200 Boots (Etsy, AntiguaHouse), $44 Highlander Spec Ops Gloves (Amazon), $30 Upper Belt (Etsy, DarmansProps), $53 Lower Belt (1.5" webbing from Amazon), $6 Ammo Pouch (Etsy, PlasticArmsDealer), $55 Helmet Padding (Amazon), $15 Small Yugoslavian Backpack for respirator hardware (Colemans Military Surplus), $25 Welding shield for goggle lens (Amazon), $6 Strapping Supplies (Miscellaneous strapping from Amazon and JoAnn Fabrics and using leftover hardware from the Yugoslavian backpack), $25 Cape/Plasch (Etsy, RussianGasMaskShop), $35 Shoulder and boot straps (Etsy, PlasticArmsDealer), $35 for shoulders and $70 for shins Respirator Hoses (Etsy, RussianGasMaskShop), $28 Paint, filler and sanding supplies, $80 Filament for 3D printing, $150 All in I'm at about $900-1000. I'm definitely over my original budget goal, and probably didn't save as much money as I would have liked over just ordering the whole kit from Jim. So, if you're considering the 3D printed route definitely give him a shout first to check current pricing and availability.