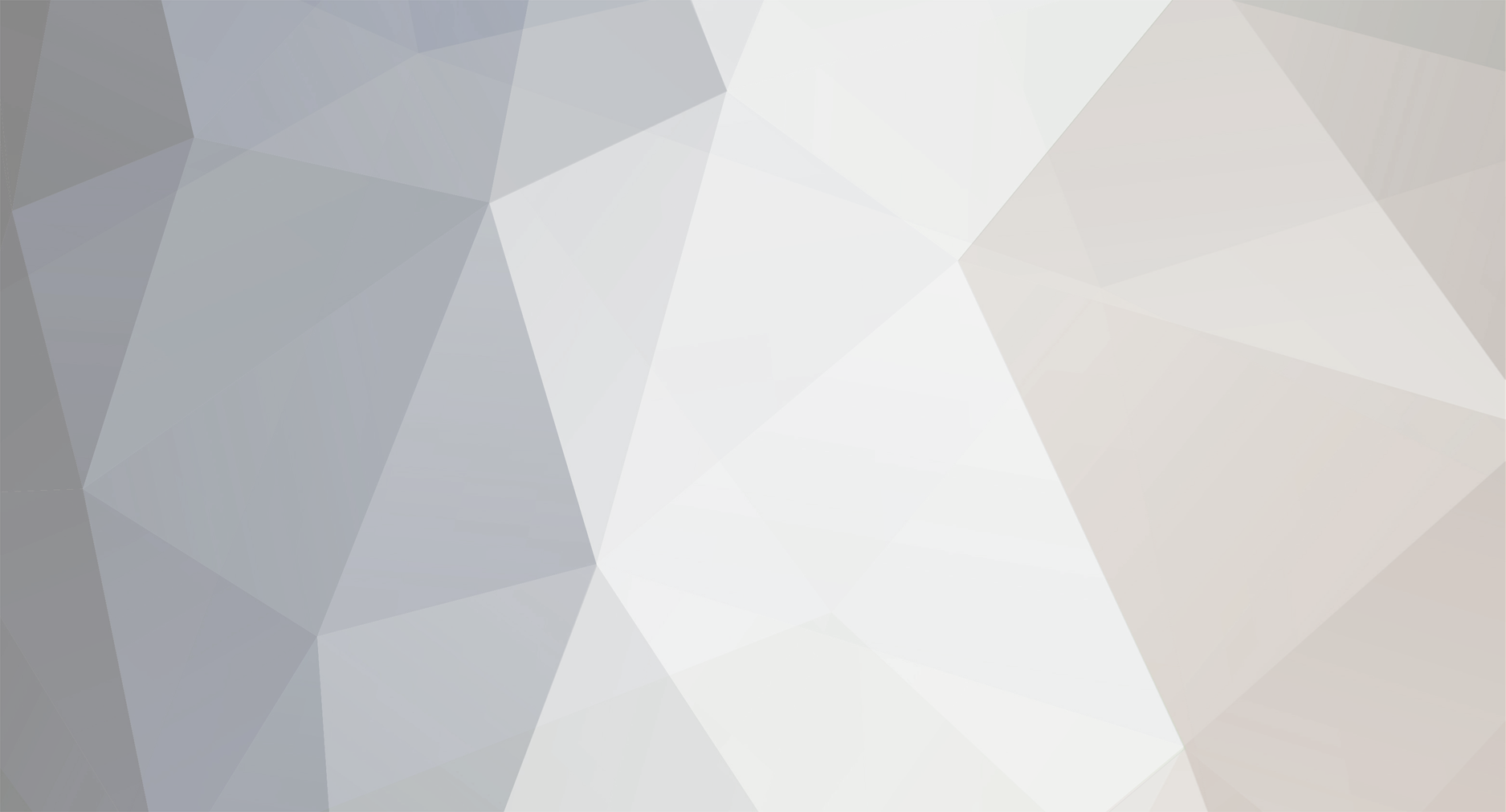
DHKnecht
Members-
Posts
50 -
Joined
-
Last visited
-
Days Won
1
DHKnecht last won the day on January 8 2021
DHKnecht had the most liked content!
501st Info
-
Name
Don
-
501st Garrison
Bast Alpha Garrison
Recent Profile Visitors
The recent visitors block is disabled and is not being shown to other users.
DHKnecht's Achievements
-
Lt. Dan - can you show some pics of how you mounted the shoulder bells with the brackets? I saw the same ones you got and wonder how they look/work/assemble. Thanks!
-
Congrats! I had no doubt you'd be the first Lvl 2 DT!
-
As many of you know, the scope mount for the SE-14R that comes with many of the 3d files and kits comes in many different flavors and sizes. I purchased Tom Campbell's files and it came with a square block for a scope mount. It works, and the scope mount is actually hidden by the belt loop in the holster. However, if you remove the blaster from the holster, it's just a square block, not the "T" shaped block that it should be, and doesn't have the inset oval details on the sides. Therefore, I created a 3d .stl file for printing that includes these details. I also added holes down the center that are countersunk for M4x30mm or 35mm screws so you can screw the mount into the barrel (after drilling holes in the barrel). This gives better strength to the attachment point, as this is the only attachment point of the scope/scope mount to the barrel/base. Anyway, I will distribute this file for free to anyone who wants it, just send me PM here and include your email. Feel free to print as many as you like for friends, etc., but in no way do I give permission to any maker or retailer to include this in any kit for sale. If you do, you must seek permission from me first. Basically, I want this to be given out for free to anyone who wants it, not just to have someone else make money off of it. A pic of the rendering is attached.
- 1 reply
-
- 3
-
-
I didn't do an 850 kit, I 3d printed mine from Tom Campbell's files. However, someone on Facebook posted a similar question about whether people painted their 850 kit, and if I remember right, almost everyone completely painted the 850 kit. Plus, if you are having to paint it anyway to cover scratches and fixed areas, it's probably better to get a uniform look, so painting everything is the way to go.
-
Although printing upside down does save on support material, to me, the cost of that material is negligible. I'd rather have a nice, solid, smooth outer surface and minimize sanding, rather than save an extra dollar's worth of support material. When I first started 3d printing, I hated wasting filament on supports. Now, I'd rather waste it on supports for a good print than have the print fail halfway through or end up with a print that is messed up and one I'll have to print again, which is an even bigger waste.
-
Those were awkward. I actually had a print fail or two getting those right, with the problem of placing them right on the print bed. Instead, I lifted them off the bed by 1/2 mm or so, so that I got supports built up underneath. There are a lot of supports here, but you need them to get a successful print with good detail on the exterior faces. The pic below is how I positioned them on the build plate. It helped to have Simplify3D so I could add supports where I wanted them, then play around with print times and filament usage.
-
CyberNinja's Death Trooper Build WIP
DHKnecht replied to CyberNinja89's topic in Imperial Death Trooper
I'm in Louisiana, so I feel your pain. I'm working on a refrigeration system for my entire unit, based in the backpack area ... stay tuned .... (should have posted that on April 1). -
Michael - just for comparison, I printed my armor on a Prusa Mk2S using PETG as well. I printed at .2 mm resolution, and for PETG, slowed the fan speed down to 30% (slowing the fan speed was the single best option I changed, and it made a helluva difference). I had to cut files like you due to the smaller size of the build plate, but I made them as big as I could otherwise, regardless of print time. The chest, for example, was cut into 4 pieces. If I could do it all over, I'd get a printer that could print the chest in on print. I spent countless hours sanding, filling, using bondo, sanding, filling again, more bondo ... all to make the seam lines where I glued pieces together disappear. Good luck!
-
CyberNinja's Death Trooper Build WIP
DHKnecht replied to CyberNinja89's topic in Imperial Death Trooper
Nice post ... keep us informed and send pictures of your build. Everyone loves seeing how the process is going. Also, I used Tom's files and printed the helmet at full size, and fit in the audio system by Tony Jobe (UKSWrath). I ordered 40mm x 40mm x 20mm fans, but switched them for 40mmx40mm x 10mm fans so they didn't take up as much space. On my one outing in full armor, I found out that fans are a MUST. It was 65 degrees outside, and felt great in full armor without the helmet on, but with it on, there was so little air circulation that it got hot quickly. -
Resizing Tom's files to fit - Who's done it?
DHKnecht replied to mjt82's topic in Imperial Death Trooper
I'm 6'0", 225 lbs., and based on what I discussed with Tom, printed everything at full size. The shins were way too long and tight, and I couldn't move in them, so I reduced the height (Z axis) only by 10%, which resulted in a shortening of the shins by 2 inches. That worked *much* better, but I should have increased the X and Y axes by 5%, and maybe even the Z axis by another 5%. I wish I had read @lancer's comment about printing just the slices, as that would have saved me some time and lots of filament. I also printed the forearms at full size, and those need to be shortened by an inch for better movement, but I can wear them now. -
Resizing Tom's files to fit - Who's done it?
DHKnecht replied to mjt82's topic in Imperial Death Trooper
Your method is probably fine. The armorsmith program is basically an estimated guess at proper sizing, which you could probably do with Meshmixer anyway. I'd have used armorsmith if it were available for the mac. Oh, and don't knock the Prusa printer. Yes, it's not able to print some of the larger parts in one go, but the print stability and output is second to none! -
I didn't mean to imply that the rivet head was a requirement anywhere on the boots. I was using that example discussed above in the split-rivets used on the TK Centurion. I'm with you IcyTrooper. The CRL has the specs for Lvl 2, and if you have the visible stitching and pull tab identical to the Jered, that should be enough for Lvl 2. The unseen padding around the ankle that is hidden by the shin shouldn't matter.
-
To Detachment Staff: You might be opening a can of worms here. If the padded part of the boots that is unseen becomes a requirement for Level 2, then what about the "corset" style of the abdomen/back plate? or the metal shoulder/side buckles? or how the shoulder bells attach? There really could be an endless discussion of detail that only the maker would know is there, and there is no real consensus on what strapping and attachment is accurate. If we later find out that no velcro was used anywhere, and it was all snaps and buckles, will we have to redo all of that? Is that what Level 2 is all about, or is it more for accurate *visible* detail? Personally, I'd stick with Chaos statement that it is only what is actually seen and visible, rather than what is underneath. As to the boots, Jereds and the replica "Killer" boots from Imperial Boots both fit the bill of course. If you want to modify a Mayer or Talib (or other boot) so that visible details are identical to the Jered, then that should be good too. Otherwise, people will be spending money buying new boots or modifying something that no one will see. If you bring in the "split rivet" discussion, the argument there is that the rivet head can be seen, and using the right type of rivet adds to the level of detail (even if you have to show an unseen area to prove it's the right type of rivet). yes, that might be splitting hairs, but at least it's a distinction.
-
Resizing Tom's files to fit - Who's done it?
DHKnecht replied to mjt82's topic in Imperial Death Trooper
I have used Tom's files and had very little need to resize, as I'm 6'0" and 225 lbs. However, what looked to be fine "as is" on the shins turned out to be too long, and I had already printed both completely. To reprint, I used Simplify3D and shrunk them by 20% in the Z axis. I probably need to do the same on the forearms, as they are a little bit long, but those can wait. I also used Meshmixer to cut the pieces before slicing in Simplify3D and printing on a Prusa Mk2S. I can't recommend Simplify3D enough, even though it's a $150 purchase. With Simplify3D, you can really play around with the position of parts, supports, etc., and not have to wait on a 5 minute time to re-slice. It's super fast, and allowed me to play around and get the best surface for each print to reduce sanding, get the best detail, etc. PS - I had heard of ArmorSmith mentioned by Lancer above, and wish I would have used it, but since I use a Mac and it's a PC only program, I never really looked into it. -
Death Trooper 3d print build in Melbourne
DHKnecht replied to Damo Fett's topic in Imperial Death Trooper
I second Woodo007's comments. I've built the suit from Tom Campbell's files and they really can't be beat, though the future files hinted at above look promising. I looked at the D03d files and see where you will have problems in accuracy, not to mention the unknown issues in printing. Tom's files print great, and are the basis for pretty much every vendor out there who sells pre-made fiberglass or plastic kits. They really are that good.