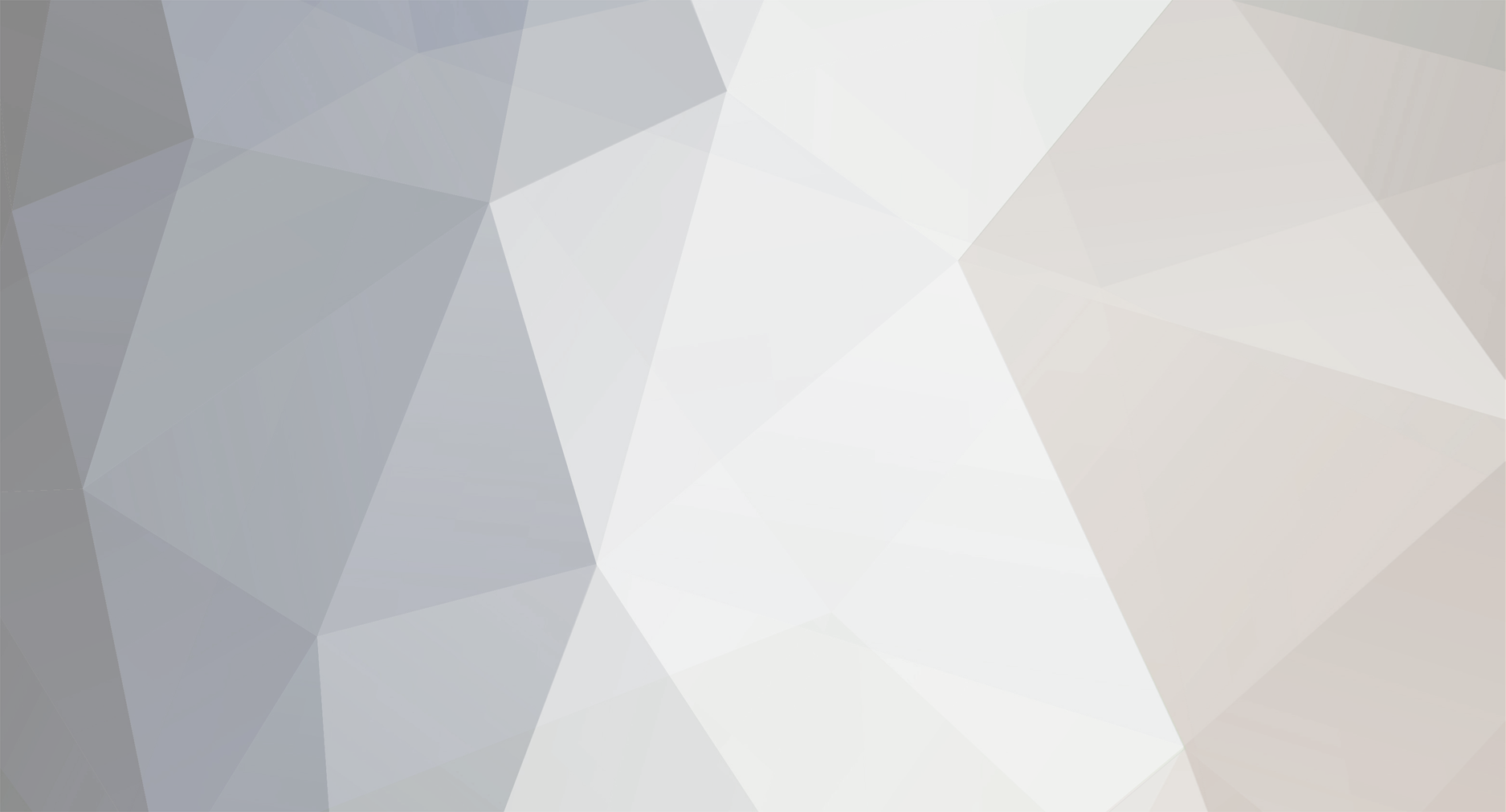
mr0072003
501st Reserve[501st]-
Posts
257 -
Joined
-
Last visited
Content Type
Profiles
Forums
Events
Everything posted by mr0072003
-
I woudl rally like to have the Weathered version approved. has anyone Seen Nodoner's weathered Black Hole. Its awesome and should be used a base to start with.
-
HOW TO - HASBRO E-11 Build with Doopy Doos Kit
mr0072003 replied to mr0072003's topic in Blasters/Weapon Mods
Part 3 - Detailing and Fixing our Errors Things You will need 1 - Dremel with Cutting Blade 2 - BONDO Glazing and Spot Putty 3 - 800 - 400 Sand Paper (You can go even to 1000 to really smooth it out, I was too impatient) Step - 1 OK Next thing that had to be done was to cut off the rest of the barrel tip of the gun. Be careful here as you do not want to cut off the wires that connect to the light. Just pull the wires out of the little groves that are holding them in place and get them out of the way. Pull them out of thw way all the way back. You can use a screw Driver to remove the glue that is holding the wires in place. This is an option but it helps not put stress on the wires. Here it is after you cut it. I used my Dremel with cutting blade. Step 2 - Next thing we want to do is to BE CAREFUL with all of the Electronics of your blaster. I did a quick check of my trigger, lights and sounds just to make sure that the gun was still working and thats when my build came to a crashing halt. The gun was no longer making lights and sounds. I checked everything and after 30min of inspecting I realized that when prying my gun open earlier in the build process, the Chip board came a little loose. I noticed that early in the process and I just placed it back in its slot and moved one. Here is the Chip in the slot Well now that the gun was no longer working I looked at the board closely and reaized that the board was chiped on the corner. With out re-explaining everything I was able to get some help from the FISD boards and got one of the master minds behind the ADURINO Blaster builds from Italy to help me out. He told me to solder a wire from point a to point b. He even was nice enought to post a pics with a drawings on it. Here it is. For all the fun details here is the link to the thread on the FISD site. http://www.whitearmo...buy-replacment/ But I was able to get a wire from an cell phone charger and have a buddy of mine solder the wire to the points listed above (the blue line). And it was working again. I was just so excited to get it working again that I totally forgot to take a picture of it all fixed up. But I did exactly what I was told to do and it worked. Now I was able move on! Step 3 - Now it's time to fix all the cracking and fill in all the screw holes with some of the BONDO GLAZE and SPOT Putty . You can get the stuff at OSH Hardware or Auto Parts store. Im sure even Home Depot or LOWES has it. You will need a spreading stick ( I used a peice of ABS plastic strip) and begin to start to fill in the holes with the putty. Also dont forget to do any seems that you do not want visable anymore. You can see in the next pic where I Filled in my extra hole. I used a bit of Hot Glue in the back and let harden and used it a base for the putty to harden on to. If I had not done that the putty would have just fallen through. If your really particular about lines and stuff take your time on this part, It will take a few more coats of putty and sanding before you get a nice even look. Again I rushed it and did an ok job. Remember that Fin that cracked on us. Now use the putty and fill in the cracks. I ran my fiongers and gave it the look you see below and let it harden before I sanded it down to look even. Fill in the screw holes good. Let all that stuff harden for a day. Step 4 - Now we can sand and re-putty if we have to or want to! Starting with the 450 sand paper for any hard and thick hard part and moving QUICKLY to the 800 paper and higer for fine sanding, you want to get you parts nice and smooth. You will notice that this stuff grinds down quickly so be carefull. Here are some shoots of my sanding work. It was not the best and I could have gone more but was to excited about moving foward. So my advice "Be Patient"! You may not want to do the handles (as seen in the pic below) as it takes away from the detail of the handle. In retrospect I would have left these holes alone. Do not fill in the holes for your Battery Compartment! At this point go over your gun with Sand paper and smooth it out to your likeing as the next part will be the Doopy Doos add ons. Yippy! -
Steve I am begining to smell an armor party my friend. I think my suit is to the point that I need the experts like your selves and really scrutanize my belt system. Are you in SoCal?
-
I would but need more of an example to see it in my head.
-
BIG THANKS for all your input guys. I took all your feedback and began to get to work while getting ready for work.. . Right now I am soo into this, its too much fun. So things I worked on Raised the thighs up and moved shifted them over a bit (much better) you can see that my thighs no longer go into my sniper plate... Next was adding a snap button next to the holster section on my abe peice, so that the holseter would not drag doen my belt on that side I added a strap set up for my AKER and iComm system in my chest plate. Fitment went perfect and in the pics you can see it does no bulg out and my chest peice lies flat against my abe peice. NExt was to bend the belt using a hair dryer. This was scary and I made a few surface cracks while doing so, but the result was the fitment was WAY better. I also cut of the edges and tried to eye a 45 degree angle. I am sure it was too much. I worked on the placement of Foam on my forarms. The foam was making the forarm bulg out, like Darth and some others noticed. So it should be sitting flush now Finally I kinda of worked on the Biceps, but It looks like I will have to add some lenght to the strap that hold its up, as it should go done further like others have noted. I will do this, this weekend. The last thing i will work on will be to have my back go down further on the straps. Now with my AKER and Icom in my chest it seems that the back plate likes to ride up and flare out a bit. Fixed easly by push up on my chest plate, but would like it to not happen as much, so thats another tweak. and of course still waiting my Akryal Bucket.
-
Blackhole / Shadow Stormtrooper Reference Pics Discussion
mr0072003 replied to izzi's topic in Shadow Stormtrooper
So i found anohter on Star Wars Wiki of Shadow Trooper looking pretty weathered. Sort of like the Side Show version. Could this be another confirmation that Weathered troopers could some day make it into the 501? or that Bicnoculers can be an optional accessory? Or this is just some fan made thing? -
HOW TO - HASBRO E-11 Build with Doopy Doos Kit
mr0072003 replied to mr0072003's topic in Blasters/Weapon Mods
Part 2 - This part will focus on the Detailing and prepping of your HASBRO E-11 TOY GUN too look more realistic to the actuall E-11 blaster. Things you will need. 1. Hasbro E-11 toy Gun 2. Dremel with Cutting Blade, grinder and Cutting Bit 3. Small Files 4. 400 Grit Sand Paper (or close to that) Step 1 (continued from my first post) Not that the guns is all apart, we can focus on the details of the gun. The first thing that I did was to sand off all the lettering from the gun. Keep sanding until its all gone. Step 2 Next thing to do, to add some realisim to the gun, is to dremel out the scope rail. The Hasbro version has the rail filled in. So following many others ideas, I decided this was easy enough to do (especially with it apart). So here is what I did (to both sides) Now that both sides are cut out, you will notice that cuts are pretty rough and jagged. So I got a small file kit and started to file down all the edges so it could be nice and even and smooth. Repeat to both sides. Try and put the gun together (dont screw in, just fit it) so you can see if there are any other spots that need filing. Step 3 NOw that the rail is cut out and looking good, now its time to grind off the 7th fin, as the real E-11 had only 6 fins and not 7. So to try and get it closer to the real thing and if your shooting for EIB, this is the next step. So using your dremel swap out the cutter tool with the grinder tool. And begin to grind off the fins like so. Step 4 Now that the 7th fin is grinded off, we will need to add HOLES in its place, this is how the E-11 looked like. So using a refernce pic as to where the holes should line up, I was able to print it out and tape it to the gun. Like so. I used a light to help me place it better. You can see it lines up nicely. Note that this is done to only one side of the gun. (use pic as refernce as to which side to use) I got the templates from this thread. http://www.whitearmo...er/page__st__80 and the best Build Thread out there that I saw was this one. But its a FISD HOW tow and thought I would post one specifically for us. http://www.whitearmo...her-hasbro-mod/ Once your template is in place, we can begin to start drilling. As first I made pilot holes using my dremel with a cuttng bit. (small) Next you can get the Drill Bit and begin to cut ( AS of this writting I do not know what size this bit is) I was just lucky enough to have it in my junk drawer and it was a prefect fit to the holes that were already there. When you are done it should like this. BUT without the first HOLE (closest to the barrel) its an extra hole that I should not have added. (again dont worry we will fix this in the next part) Step 5 Now that our holes are complete, lets work on the last little detail. The Trigger, this was one I was on the fence on, but it seemed to easy to pass up, especially with the gun apart. SO using some refernce pics, I was able to draw up a sketch using a pen. Then I started to cut at it with the Dremel and Cutting blad. Here is how it ended up. Used the file to clean up the edges. Thats it for part 2. Next part will be the prepping and cleaning up of any mess ups that I did. -
Hi all another step by step of how I did my build of my HASBRO E-11 Doopy Doos mod as promised that I would like to add to the site. Thanks to all the other HASBRO Build threads on the FISD site as each one was helpful in differnt ways. I thought it would be nice to gather all the info from all those threads and make my own HOw to Build Thread. I will show as much as I can errors and all. Part 1 - This part will focus primarly on how to take the gun apart. Things you will need. 1. Hasbro E-11 toy Gun 2. Small Head Flat head screw Driver 3. Phillips Head Screw Driver 4. Exacto Knife So lets get started. I ordered my E-11 Blaster from E-Bay for $8 Buy it now and $8 shipping a Total of $16. It was a Star Tours Version which is the same as the Other HASRBO E-11 but in Black and White tone, not the Orange and White. Here is the pic of the balster I purchased. Step one. First thing we need to do is to remove all the screws from the gun, with a Phillips Head Screw Driver. There will be a total of 11 Screws. 2 of them will be smaller than the rest. They are from the Tip of the gun (Site and Bottom portion of the barrell). Step 2 You may notice that the gun will not open even with all the screws out. Well thats becuase the next thing that had to be done to get this open, was to pry my Scope Cap off. While researching this is the part many had issues with and did not know how it was done. Many posted how they did it, but did not show. So here is how I was able to pry my Scope Cap off. Work it all the way around very slowly but firmly. Dont go to hard, or else cracking and or breakage could occure. AS you can see in the pic below, there was some minor cracking. (Dont worry we can fix this later.) Once you work it all around you should be able to get it off like so. Step 3 (Optional) I did the same process to the Cap in the front of the scope. If doing the Hasbro Doopy Doos mod, this part just gets cut off but I was not sure at the time, as I had not got my kit when I started to pry apart, so I did it be safe. I am showing this step just so other can see. Step 4 Well now that we have the Screws off, and have removed the caps from the scope. We need to cut off the front portion of the gun (the orange tip) also. NOW I know that we are to remove the entire front portion, but again I was afraid to as I did not have my DOOPY Kit at the time, so I only cut off the Orang tip. Here is what I cut off. You can see I tried to pry the orange tip (SO I would not have to cut) but I decided to hack it off, as I was pretty confident at this point that it needs to get cut off to add the doopys barrel tip. Here it is after I decided to just cut it off. Step 5 This is the part that most people dont even mention (Some do) but not all, and thought I should share this experience. What needs to be done after the all the parts that are holding the gun together is to pry the the glued seem of the gun apart. This is where my troubles started. So I decided to go at it with the same small Flat head screw driver, and quickly realized that this was damaging the gun quickly as seen here. So change of plans, and I went at it with an Exacto Knife. Did this all the way down the bottom portion of the barrell Like so So now you can start to pry the gun apart, but you may notice that the top fin is also glued together and may start to break a bit. (Dont worry if it happens, we will fix later) So be careful (also be careful when using the exacto knife, as you can see in the 1st pic below I cut myself pretty bad) Now pry the back part of the gun, You should not have to use the exacto here, but all cases are differnt. You can see that it comes apart like so! After all that the gun should open up like so.
-
Thanks everyone. I feel better about this tut now. Yeah I left the placement for interpretation, but I obviously placed them to high. I was able to grab this from the FISD site and thought since everyone here thought it was a good post, I thought I would update the end of tut with this image so folks can know where exactly to post next time. Had I not got a stunt helmet I would attach the other rivets making it a hero style holster, but I do not want to mess up my EIB or specialist goal with an obvious errors such as that.
-
Part 2 - Step 6 Now that we have pinched the plastic tool to the holster and belt; Using the Mallet/Hammer, and hammer the tool together so that they can picnh the rivets together. Like this: Once you have hemmared and piucned the the rivets in place you can remove the plasti tool and the rivets are now in place like this. Here is the front Here is the back Repeat these steps to both sides and your holster will look like this. ( I went ANH STUNT, but i placed my rivets to high) I have added a great image as to where the Holster placement should be and how long straps are etc. I wish I would have seen this first and I would not have made my mistake, but the process is still the same just place correctly (Pic reference from FISD site) I hope this helps some one out there.
-
Hi everyone, as promised I have set to do another How To and place them here to the forums. I just feel it's the least I can do to give back to a community that has given back to me on this project. So lets get started. As with much of this build I found that the stuff I thought in my head would be easy, turned out to be harder or more steps than I thought. So with attaching the belt I thought it would be easy (and it is, after research) but when I started to actually think about how to do it and where to get snaps rivits etc, I noticed I have no clue what I am doing. I searched and found many post on what to do as far as how to attach a holster, but never did I find one that actaully showed how to do it or what they used and where they got the supplies from . So here it goes. Things you will need. 1. Rubber Mallet or Hammer - (Home Depot, LOWES, etc) 2. Jean Rivets (5/16 or 7.9mm) – (Michael's) 3. Jean Rivet tool Kit - (Michael's) 4. TK Style Holster – (www.StormTrooperundersuit.com) 5. Canvas Belt – (www.Trooperbay.com) Step 1 . First thing that needed to de done for my particular holster that I received from www.stormtrooperundersuit.com was to cut off the loop portion so its no longer a loop in two places on both sides. Here is what the holster looks like. Here is the loop part we will be cutting. Here is the first portion that I had to cut, this is the one closest to the rivet that is connected to the base of the holster. Here is where I cut on the second part. It's where the loops folds over. Here it is after both pieces are cut off leaving you with only one piece. Repeat to the other strap on the ohter side. Step 2 – Now that you have it all cut up and left with a single strap on both sides, we can now begin to test out the placement of where you want to place your Holster. Here is when you can decide whether or not you are going to ANAH STUNT (has only 2 rivets to hold in place) or be a ANH HERO (version that has 4 RIVETS. Please note that whatever way you decide to go, the holster is to be attached the holster with rivets from Behind the canvas belt. Here is a pic of my placing the holster behind my belt and trying to find the best place to attach the holster. Step 3 – Now that you have figured out where you are going to place your holster, you need to attach it to the belt. And this is where I started to get stuck. As I read and researched I noticed that people were using split rivets, snaps with rivet style backings, even Chicago Screws. I was overwhelemed at what road to take and having no luck finding split rivets (except for online). So a trip to Michael's ( I was looking for a hobby anvil) I found something that looked like exactly I was looking for. Here it is – Jean Rivets Then I realized that I would need some sort of tool to attach these, (like snap systems does) and sure enough right next to the Jean Rivets was the Jean Rivet tool kit. Here it is – Jean Rivet Tool Kit I bought them both and took a chance that they would match the rivets on the holster already. So when I got home and checked the size against what was on the holster, I was happy to know that they were an EXACT match. Here is a pic of comparing the rivet on the holster to what I bought. Pretty close right? Here are the rivets front and back before attaching them. OK so lets attach them! First thing you need to do is to hole punch a hole in the canvas belt and holster strap at the same time. You can use the hole punch tool that came with your Jean Rivet kit.. Here is a pic of the hole puncher Then you attach the hole puncher to the plastic holder that also came with the Rivet Kit. Like this Now place your hole puncher to the area you want to attach with rivet against the top of the canvas belt and the holster strap directly behind it (placed where you want it) so that we can punch a hole through the Canvas belt and holster at the same time. Like so Using your mallet or hammer begin to punch the hole puncher through the belt and holster. Use a hard surface. It should end up looking like this once it's through. Step 4 - Now that the hole has been punched through both the Holster straps and the Canvas belt, and make sure you can push through the male portion of the Jean rivet like so and that there is enough room for the female portion to snap it together. Now that you have verified that the male part pushes throught the holes, we can use our plastic tool and two rubber/metal groumets that are used to punch the Jean rivets together. (comes in the kit) Here are the groumets and plastic tool. You will need to attach the groumets to the holes on the plastic tool . Like this - Notice that one groumet has a dent in it. Now we need to add the Female part of the Jean rivet to the groumet that has the dent in it the male portion on the other side Like so: Step 5 Now lets punch the rivets so that we can attach the holster and belt together. So lets pinch the plastic tool with the rivets inside them to the holster and belt. Like this
-
Yeah the Helmet I will be getting will be from Arakyel. Those are approvable right? EDIT - Update My wife was able to use here new D5100 camerea I got here for Xmas but was only able to snap two shoots as she is knew using it. So I have some clear and better pics, only 2 and sadly I know my chest plate is stickout cuz of my amp, but otherwise it does sit flush against my body.
-
Here are some more pics..... please any feed back is welcome, as I know there is stuff to tweak!! I am concerned about the holster placement, and if my belt hangs to much to my left side because of the holser (more snaps?)
-
UPDATE ON THE PICS OK guys I got my doopys and unsersuit order in, which also included gloves, and neck Seal. Here are some shots that my wife took. I still think I need to lift the thighs, and need to work on my AKER system and how I want to attach it to my Chest plate. I have a few ideas, just not sure what Route I want to take as my first set up was a failure. Please ANY FEED back is welcome. I will also post on my intro thread in case other are following that.
-
HOW TO - Make your shins not shift
mr0072003 replied to mr0072003's topic in Miscellaneous Tips and Tricks
thanks Guys. Yeah I have been waiting for my Undersuit and accessories from stormtrooperundersuit.com for over 2weeks now, as well as my Doopydoos HASBRO conversion kit. (Sigh). I hate the waiting, and I just read about people having issues with DOOPYDOOS customer service and shipping so mow I am really worried. -
Hi everyone, with so many great HOW TO'S that helped me along my build and more importantly NODONER from here on the SEPC OPS forum for taking his time to help. He really is a great artist in anything he does, and has helped me keep my build as good as can be. With that, he had shown me a few tricks and I thought I should share and give back to the community since the parts I did do on my own, I used the HOW TO SECTION. So first thing I noticed after I got shins in place, Foam in place to keep a good fit, and my Bass Amersterdams all on for the first time and I started walking around the house, I noticed that my shins kept shift bad and next thing you know my cover strips were on the SIDE of my legs. So here is what nodoner showed me. I am sure this can be used for the TK crew as well. Things you will need. 1. Industrial Strength Velcro 2. Some left over ABS from your build 3. Dermal or Cutting tool 4. Boots 5. Shins from your TX or TK armor. I did not take pictures of the build process from the start, so apologies in advance. Step 1. Grab a piece of left over ABS and Cut it to about a tab length. Almost like a rectangle. This may differ depending on what types of boots you have, but most boots are the same. Step 2. (A few) Once you have cut a rectangular strip, you will want get your industrial strength Velcro loop and it stick it to one side of the tab. The Other side can also be loop but will be longer than the actual tab; this is the part that will hold on to the inside of your boot. Make sure to use loop and NOT hook here. Your finished product should look like this. Close up of the Tab Tab stuck on to the inside of the boot. Make sure to stick it on to the front part of the shoe. Step 3. The Bass Amsterdam's that I bought have tabs on the back of the shoe. We will use this tab to add a strip of our Velcro (Loop) to it, plus a little more so it goes a down a bit. It should look some thing like this. Here is a close up of the tab with loop stuck on. Here is a side view to give better viewing perspective Step 4. Now get your shins! We will be adding the HOOK portion of the VELCRO to the BACK side of the INSIDE part of the shines. I added a lot of HOOK to and I used the wider stuff to give myself more room to adjust. If you want to be more precise about it, just put on your shoes and shin and mark were you need to apply the hook once you have them on. Here is a pic of the inside back part of the shin You will need to do the same to the FRONT portion of the shin as well Here is a pic of that. I used the overlap method, but I am sure strip cover backings will have no issue here either. Step 5. Now that yoy have all your Velcro in place, you can try them on. You can even them connect the shoe to the Shin and the shin will stay in place. Here I am trying them on and running around my condo like a madman. (I was making sure that they don't move around of course). And they didn't. (I have not completed my suit as of this build so excuse the missing under suit and AM helmet.)
-
Thanks everyone. Its been fuin working on this thing. I spent this last few weeks just cleaing it up a little bit and adding covver strips to pretty much everything that needed it. I used the overlap method, but after some research found that the strips would look better and much more accurate to a TK ( i know im a tx). I also created a v cut on the back of the shins to allow for more movement. I figuerd since the stunt version has them like that and is 501 approved. Few more updates - I recieved my AKER Voice amp and iComm set up and LOVE IT. I also just received a HASBRO E-11 that I bought from Ebay. I alos got the Doopdoos conversion kit, but that has not arrived. Finally I tested the armor yesterday as I also got my boots on Xmas (Bass Amsterdam's). Still lots to fix, Left Shoulder bell placement. Need to get my Canvas belt (in the mail from trooperbay), need a better bucket as the AM buckets are no longer 501 approved. (admins correct me here if im wrong, i dont want to spreead rumors based on me misreading another post). Still need my understuit, neck seal, holster, golves.... Need to glue on the final Button to the abe plate, then paint them black.... Sigh as I liked the silver look. Man I wish I ordered this earlier.
-
HI all Finished up my helmet Saturday night. I did it for fun as I already paid a deposite for my Helmet from Akryl. I already painted the blue stripes black, but I did that later the next day befoer I took the pic.
-
i knew it!!! I figured the stripes would help me out, but im surly not getting in the 501 now. DAng!
-
as promised more pics.... Here is a closer clearer pic of thighs I think I glued incorrectly. here some close ups of the snap system etc as you can tell, i made a mess with the glue. I let it happen as I am going to go weather (i think) unless someone here knows a good polish that could get these rough parts sanded and buffed out again. I just dont know with black. My wife wants me to stat shiny. I am still on the fence about it. I teeter back and forth on it actually.
-
HI guys Just wanted to update this thread a little. I have completed many things over the past few weeks. I completed the Thermal Detonator, have completed glueing and cutting all of the pieces, that needed it. I have complted the snap system for the front and rear chest plates as well as the shoulder bells and biceps. I have halfway completed my ab and kidney plates, but still need to add the buttons snaps for the cod and butt peices and thighs. After that it will be closing up any loose parts and trimming parts to allow for bettter movement, all of the strip peices, getting Foam for the forarms, ammo belt, batterpacks,...and anything else I may have forgot. also I have a feeling I peices together the wrong thigh pieces and afraid that they are backwards. Can anyone confirm?
-
nice. I have been working on mine all day today. took the day off.. Looks great and cant wait to see your progress!
-
Yup i have that too. My budy lent me his, and its awesome. I will post pics later.